Clocks Magazine Finding faults in clocks |
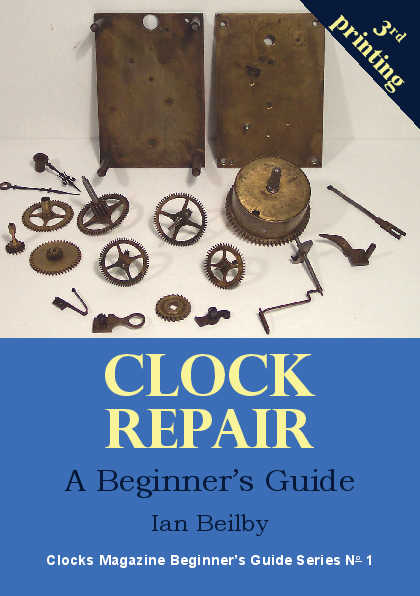
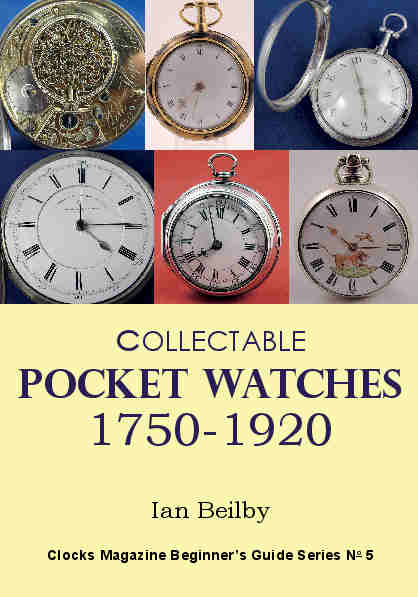
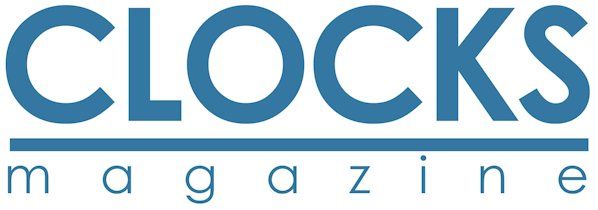
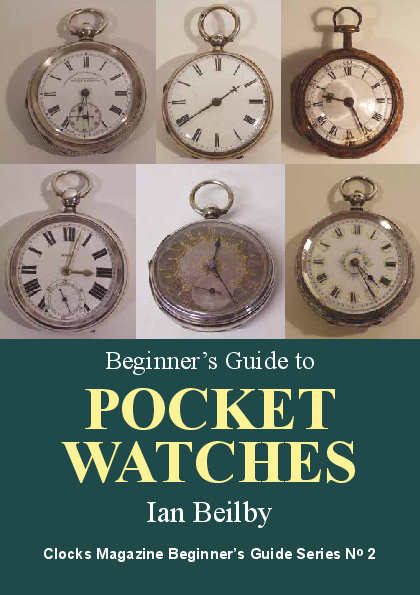

Clock fault finder 2 Dismantling the movementBefore dismantling and attempting to diagnose the faults of any clock movement, you must have a good understanding of the operating principles of a basic clock movement and in particular the type of movement you are working on. The movement should be removed from its case and its condition assessed. If it is clearly dirty and there are visible signs of dirty congealed oil, it will certainly require dismantling and cleaning. With the power removed there should be an audible and visible shake to all the arbors when the movement is shaken. This is called `endshake'. If the movement is a striking movement, check that the striking train is releasing and working correctly and is not causing the movement to stop. Remove the motionwork and striking detent levers. With the power removed and finger pressure applied to the great wheel, worn pivot holes become very evident. Any worn pivots can be seen to move excessively in their holes. The pinions should be checked for 'pocketing' or wear. A combination of badly worn pinions and worn pivot holes can affect the depthing of the wheels and the efficient transfer of power from the motive force of the train to the escapement. If the pinions are very badly worn the meshing wheel may have to be moved on its arbor. The escapement must function correctly: all power from the mainspring/weight must be used to drive the pallets and pendulum. As one tooth of the escape wheel is released by one pallet, the next tooth must be arrested by another. If the clock is spring driven remove the mainspring and examine the spring. Even if the spring is not damaged or fatigued there is always the possibility that it may have been replaced at some time by a spring of the wrong size or type. Having thoroughly cleaned and re-assembled the clock, check the movement plates are pinned up tightly and that there is noticeable endshake between the shoulders of the arbors and the movement plates. With the pallets ensure the train runs freely with no sudden stoppages. The wheels should spin freely irrespective of the position of the plates. The movement should be rotated and turned upside-down and the wheels should continue to spin regardless. Any sudden stoppages should be investigated and the cause rectified before proceeding with the assembly of the rest of the movement, motionwork etc. If the running of the train is giving problems, try the wheels individually then and in pairs. Check very closely the depthing of any re-bushed holes. A previously re-bushed hole may not have been re-bushed accurately, causing the wheel/pinion teeth to butt together. The repair may have been acceptable to start with, but after a few years running and slight wear, the faulty bushing/depthing becomes apparent and is sufficient to stop the clock. If the movement is built-up in stages it should be possible to check the running of the movement at each stage and ensure that when fully assembled the clock works correctly. When happy with the running of the going train, the motionwork can be fitted, and then, on a striking clock, the strike release levers fitted in place. Striking, chiming and calendar work puts a temporary but additional load on the motionwork and going train of the movement. The effect of releasing the strike and changing the calendar should not have any effect on the movement or alter the rate of the clock. The clock should be kept on test for a couple of weeks during which time its rate should be noted and brought to time if necessary. With everything working correctly the movement can then be lubricated and put on final test. Experience has taught me not to oil the movement until I am completely happy with the running of the clock. If the clock is oiled and has to be dismantled because of an unforeseen problem, the oil will smear the plates, which will then require re-cleaning. Although correct lubrication is most important, a clock movement should be able run `dry' for relatively short test purposes. After oiling, the clock should still be left on test for another week or so and the timekeeping finely regulated. Although the above list of likely faults and remedies is not exhaustive and there are many other possible causes for a clock stopping, a systematic and isolating approach to fault finding can help in both saving time and pinpointing the actual fault. Readers will appreciate that I have restricted my list of faults and suggested remedies to a simple pendulum timepiece movement as described in the beginners guide series. Balance wheel movements and other more complicated clocks may develop other faults and may require a different diagnosis. << Back to previous page | Continue with fault finding >> |
|